柔韌設計RFID新樣貌
ECORE Pro實現嚴苛環境下的大數據追蹤
全球首創以RFID實現晶圓無塵衣智慧洗滌管理,將ECORE Pro特殊可彎曲的彈性及高耐受性,無縫置入無塵衣中,實現可視化及IoT整合,進而達到高效率的工業4.0自動化,是邁向智慧製造的最佳選擇。
專案背景
台灣是全球半導體製造的重要基地,擁有許多先進的科技聚落如新竹科學園區等,在這個以極度高精密為核心的產業中,無塵室對於污染控制的要求細至微米等級,因此對於無塵衣洗滌也有其嚴苛的規定。路得潔淨科技(Ruth Cleaning Technology)在無塵衣洗滌管理領域已耕耘超過二十年,服務對象涵蓋半導體、光電與生技產業。 因應智慧化管理與可追溯的無塵衣管理服務需求日益提升,路得潔淨導入全球首創RFID無塵衣洗滌管理,核心技術即是ECORE Pro – 這是一種可整合於布料中的RFID解決方案,可承受極端洗滌條件,且不影響衣物功能及無塵室中工作穿戴的舒適度。

應用挑戰
路得潔淨過去以條碼進行整籃掃描,無法追蹤單一衣物,導致:
• 頻繁的衣物遺失與配對錯誤
• 人工作業失誤及修繕耗時
• 隱形成本的增加如少收費用、流程低效率
雖然早有考慮RFID應用,但傳統RFID標籤通常體積大、材質硬,在多次高溫、高壓與化學清洗後容易損壞,更可能影響無塵室作業人員穿戴於工作場域時的動作順暢度。 路得潔淨需要的是一種「可縫製於衣物中、柔軟且耐用」的RFID解決方案,能像布料一樣自然存在,並適用於嚴格規範的無塵室環境。
解決方案
ECORE Pro – 結合柔軟與高耐用於一身
為解決這個長久的難題,由台灣紡織產業綜合研究所(TTRI)與韋僑科技(SAG RFID)共同開發ECORE Pro,一款仿紗線結構的RFID標籤,兼具布料的柔軟性與工業等級的耐用性,特別適用於傳統標籤無法承受的嚴苛場景,重新定義了RFID在單件資產追蹤的應用。
主要特色:
• 超高彈性與韌性:可直接如布料般縫入衣物,穿戴無異物感
• 極高耐受性:可承受超過100次工業級洗滌流程,包括高溫、高壓、化學與機械摩擦
• 優異讀取性能:搭載 NXP UCODE 8 晶片,可於高密度標籤環境中快速遠距讀取
通過嚴格測試標準:
• AATCC 135(可洗超過100次)
• CNS 8150(縫線強度 ≥ 40N)
• ASTM D2256(拉力強度 ≥ 1 kgf)
• ISO 7854(抗彎折 ≥ 1000次)
現場實證與人體工學設計
TTRI 所進行的人因工程研究,記錄穿戴者的操作動作與姿勢,進而找出最適合安裝 ECORE Pro 的位置。現場實測證實,訊號穩定,且不影響衣物結構及穿戴者於工作時的各種操作動作。

從 RFID Yarn® 邁向 ECORE Pro 的進化
ECORE Pro 是 RFID Yarn® 的進化版,不僅具備更強大的讀取能力與材料韌性,亦可擴展應用於更多高需求場景,是智慧自動化製造的理想嵌入式 RFID 解決方案。
ECORE Pro 是 RFID Yarn® 的進化版,不僅具備更強大的讀取能力與材料韌性,亦可擴展應用於更多高需求場景,是智慧自動化製造的理想嵌入式 RFID 解決方案。
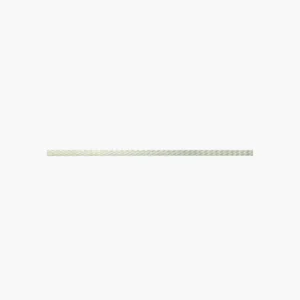
RFID ECORE Pro (Yarn-type Tag)
RFID ECORE Pro (Yarn-type Tag) features its flexible and bendable design to be embedded in non-metal items. The yarn-type form factor offers a unique way of RFID attachment to digitalize tracking and identification of fabric, cable, wire or items with narrow structire or limited space. Though in a high temperature and chemical exposure. RFID ECORE Pro opens every tagging possibility and helps create innovations with future potential.
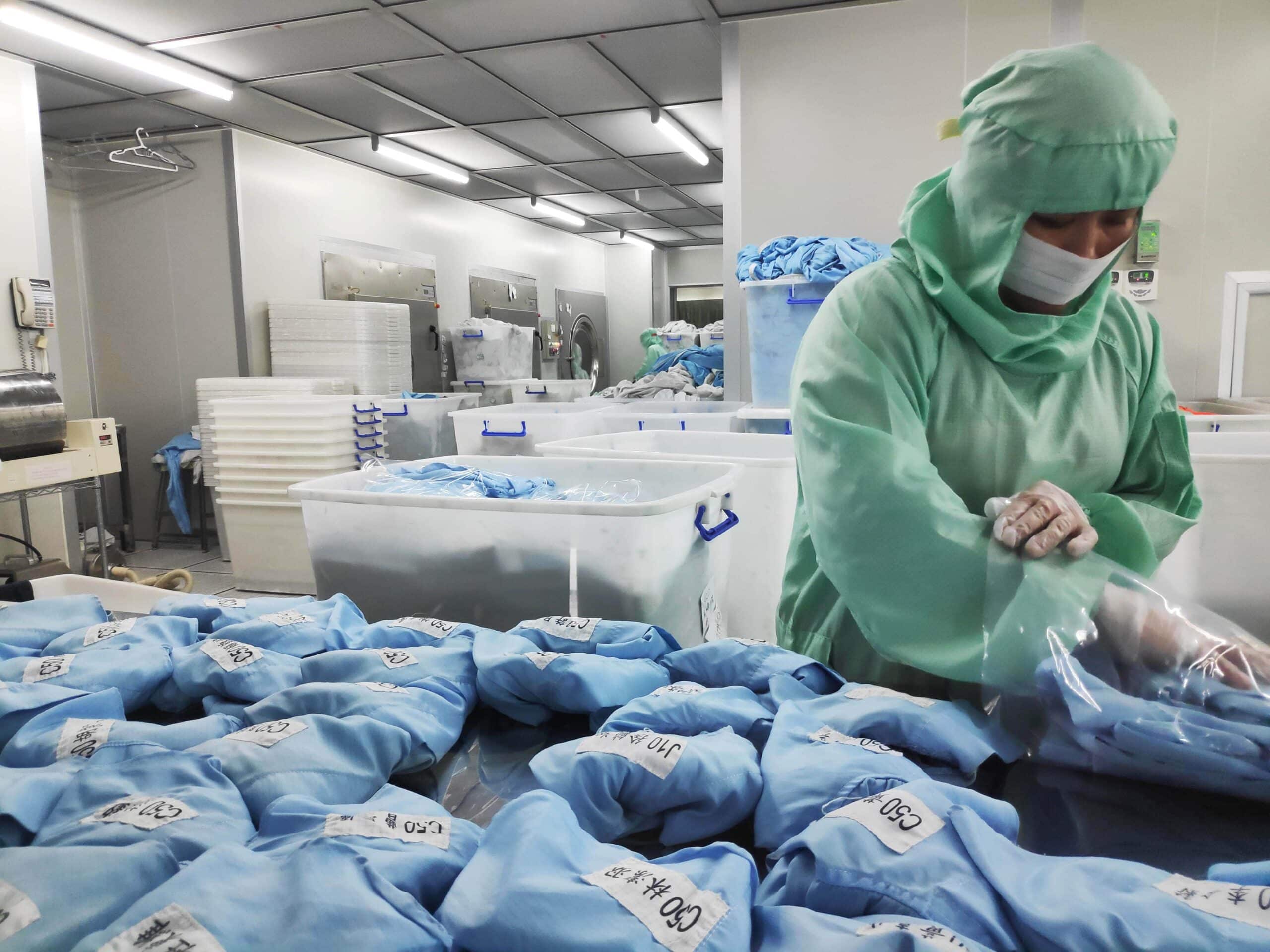
策略目標
為實現這座劃時代的創新系統,路得潔淨攜手三大領域領導者:
• TTRI:提供紡織與人體工學專業
• SAG:提供RFID標籤設計/量產與連續自動化捲對捲製程
• 中冠資訊(中鋼集團):導入製造執行系統(MES)
合作成果包括:
• 全球首座 ECORE Pro 生產線,實現高品質規模化製造
• 首套專為無塵衣洗滌流程設計的自動辨識系統
• 全面性數位轉型,實現即時數據捕捉與智慧產品生命週期管理
Play Video
效益成果
導入ECORE Pro後,路得潔淨的服務模式從勞力密集轉為數據驅動,實現單件衣物全流程追蹤:
• 收件 → 分類點數 → 洗滌 → 修補 → 包裝 → 出貨
實績(以每日7噸計):
• 處理時間減少48%
• 總體產能提升45%
• 人力需求降低30%
同時系統能記錄每件衣物的使用頻次、洗滌次數與維修紀錄,實現品質管控與客戶滿意度的雙贏。